The Rowan Magazine design process
When you receive your new Rowan Magazine, either as a subscriber or from your local yarn shop, a lot of work has gone into it. Creating our bi-annual Magazine starts over a year before you can hold your copy in your hands.
It all begins
When our management team and key designers such as Lisa Richardson, Martin Storey and Georgia Farrell get together and work on the design stories for the Magazine. They will consider everything - trends in fashion and knitwear, new yarns we are planning to introduce, and what the new shades for our existing yarns are going to be that season.
When the stories are all worked out, moodboards created and yarns selected, we send out a call for submissions to all our designers. They will be given the moodboards, details of the stories and balls of yarn to swatch with.
Design selection
After a few weeks, their submissions begin to come in by post and email. Our in-house design team love this part, as they are the first to see the submissions and pick their favourites! Once we have received all of the design ideas, it is time for the management team, Lisa, Martin and Georgia to reconvene and select which designs will be produced.
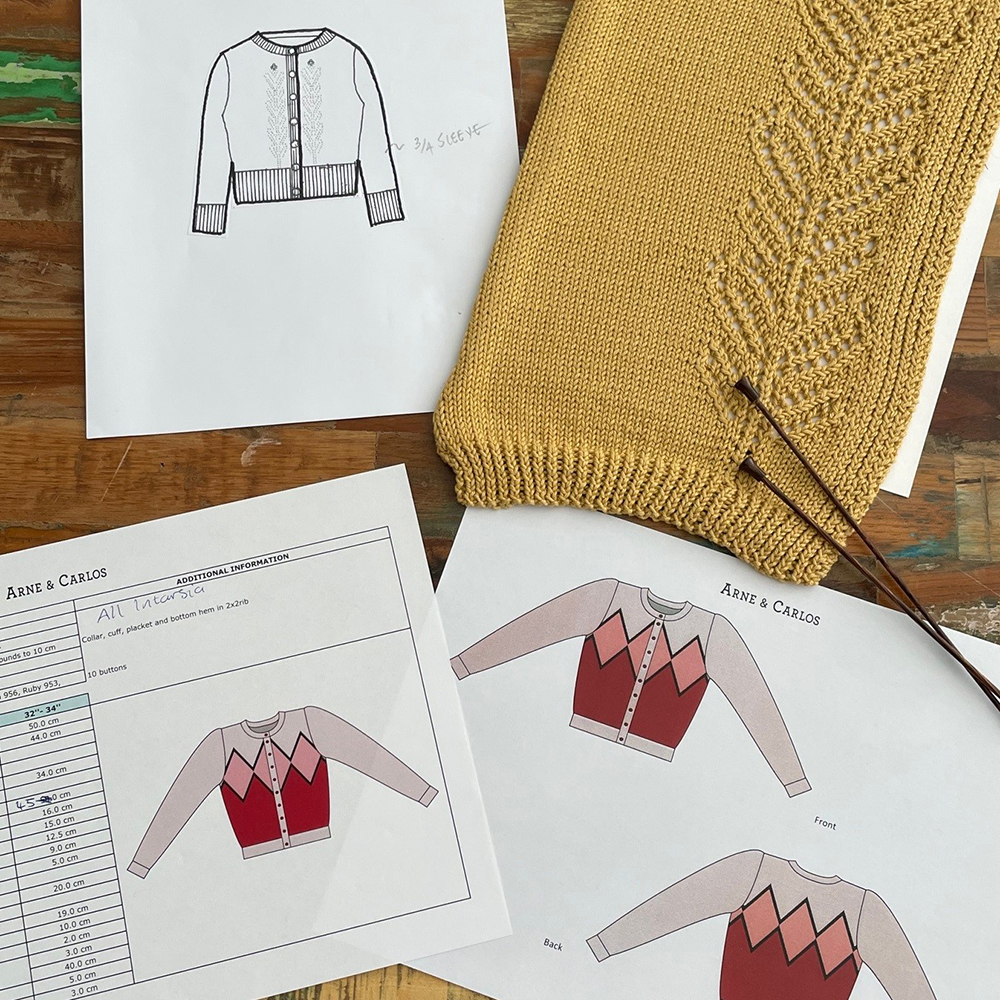
When the final selection has been completed, the in-house design team gets to work. The first step is to inform all designers about what designs have been picked. They are then asked to produce garment specs and fill out all essential paperwork. Garment specs will provide our pattern writers with all the details they need to write a pattern that matches the designer’s vision. This includes information like needle sizes, tension, sleeve and body length, stitch patterns and so much more.
At the same time, Anna, who manages the technical side of our design process, will create an overview of all the designs, fill out a huge spreadsheet that will track every step of each design from now on, and start to speak to pattern writers to manage the timelines.
Pattern writing
When garment specs arrive back in the office, they are checked and if necessary, we re-swatch. This usually happens when we know a designer generally knits tighter or more loosely than our standard tension. When all details are final, they are sent on to our pattern writers. We work with several freelancers who have all been trained to write patterns matching our Rowan style.
Some patterns might need a chart and our in-house design team create these in Illustrator. Creating a chart can take anything from a few hours to a couple of days if you are working on creating a chart for a complex Kaffe Fassett garment, for example.
At the same time, other members of the Rowan team order the yarn to knit the samples from our warehouse and contact our knitters to find the best person for the job. Rowan works with a lot of freelance knitters, many of whom have been with us for a long time. Often they have become experts in lace, colour work or cables and knit samples in record time! Usually, our knitters have about a month to finish a project, but it does vary depending on the size and complexity of the projects.
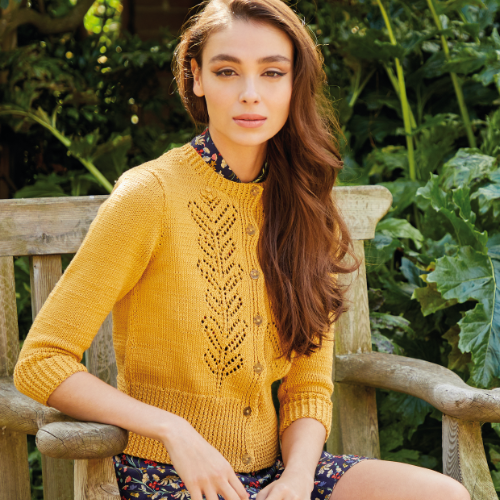
Next steps
As the garments are being knitted up, the work continues in-house. The focus now shifts to preparing for the photoshoots. Neya, another member of the design team, organises the shoot after the management team and key designers have worked out the aesthetics. This usually means finding and booking a location and accommodation, selecting models, and checking which of the photographers and make-up artists we work with are available. Another important part of this process includes styling for the photoshoot.
This last part usually happens after all garments of the same story have been returned to create a unified look. Once we receive the garments back from the knitter, they are checked against the pattern, weighed, and then sent off to be finished by an in-house team of finishers. They block and seam the garments, sew on buttons, and add any other finishing touches like embroidery.
After the photoshoot
Once the photoshoot has been completed and the garments are back in the office, Anna will organise the checking of all patterns. As with pattern writing, we work with freelancers on this part of the process. All our garments are checked by two different checkers and the accessories receive one check. The checkers also fill out a form that allows Neya and Anna to calculate the yarn amounts for the sizes that were not knitted up. This is a lengthy process using an old computer program written for us for this purpose, but it is still significantly faster than calculating by hand.
To finish the patterns off, Neya will create size diagrams which provide a schematic with the most important measurements. Meanwhile, Anna will manage the translation process. All our patterns are translated into German, French and Spanish. This also includes translating all charts.
While all this technical work is happening, the photos from the photoshoot are viewed to select the final garments and images we want for the Magazine. These are then sent to repro to ensure they are the best quality and as true to the colour of the yarn as possible.
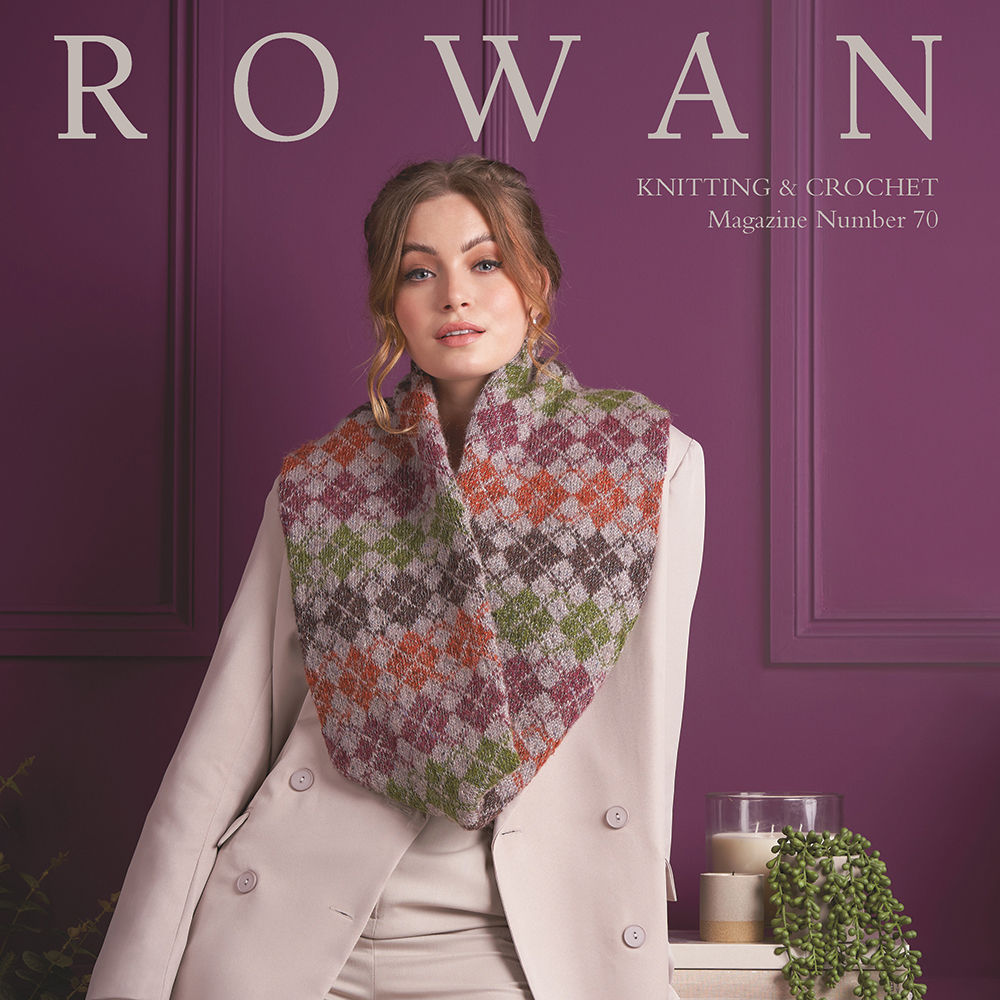
Bringing it all together
After all these processes are completed the patterns, charts, size diagrams and images are sent to Lyndsay, who is our Publication Manager. She creates the beautiful Magazine layout that you know and love. When the process is completed, the Magazine is checked by various people in-house before it is sent to the printer and ready to be received by you.